Learn more about what we do.
Considering your next construction project, and wondering whether Verto360 can help? Take a look at these commonly asked questions to learn more about prefabricated construction and all of its benefits.
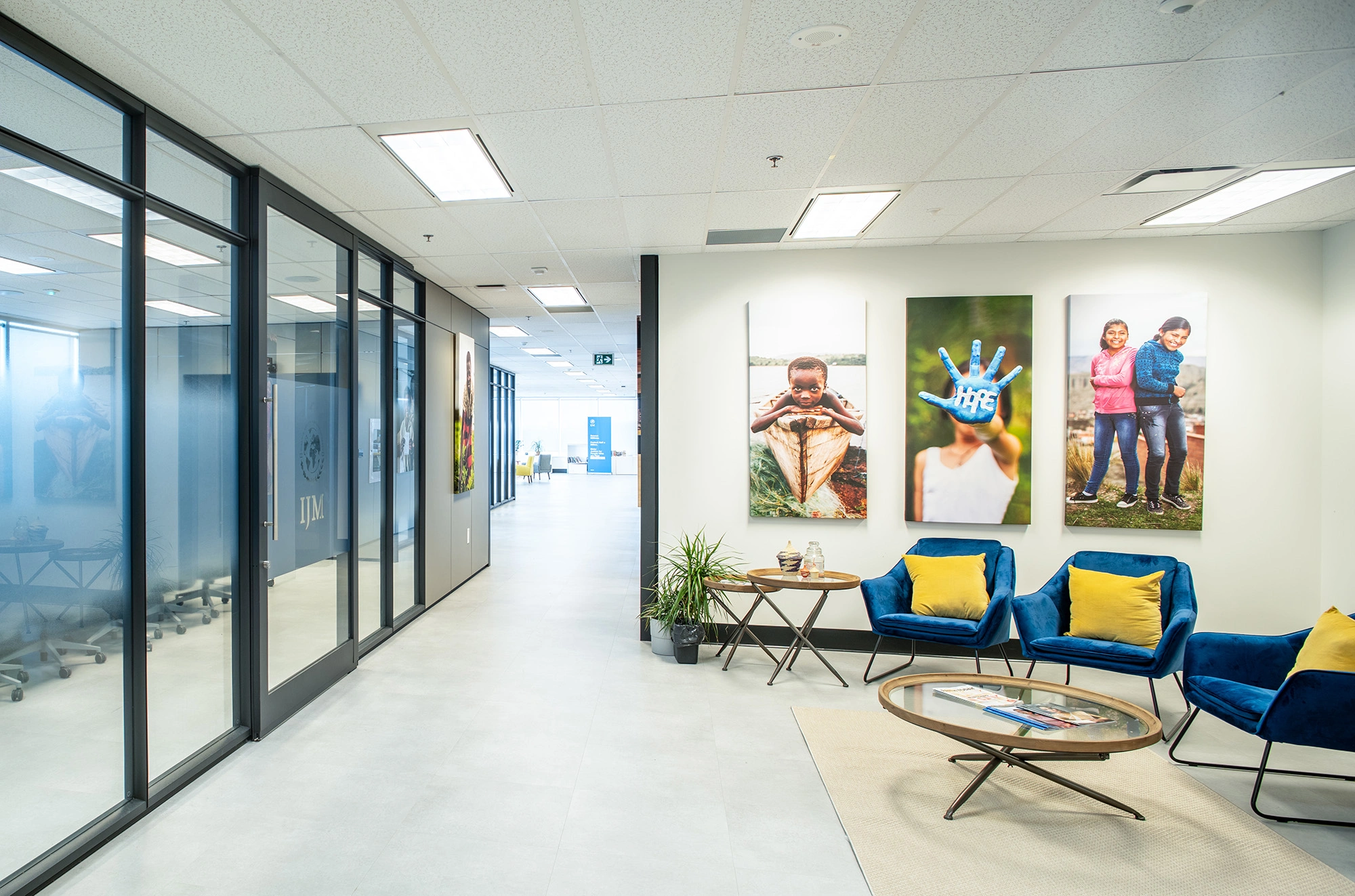
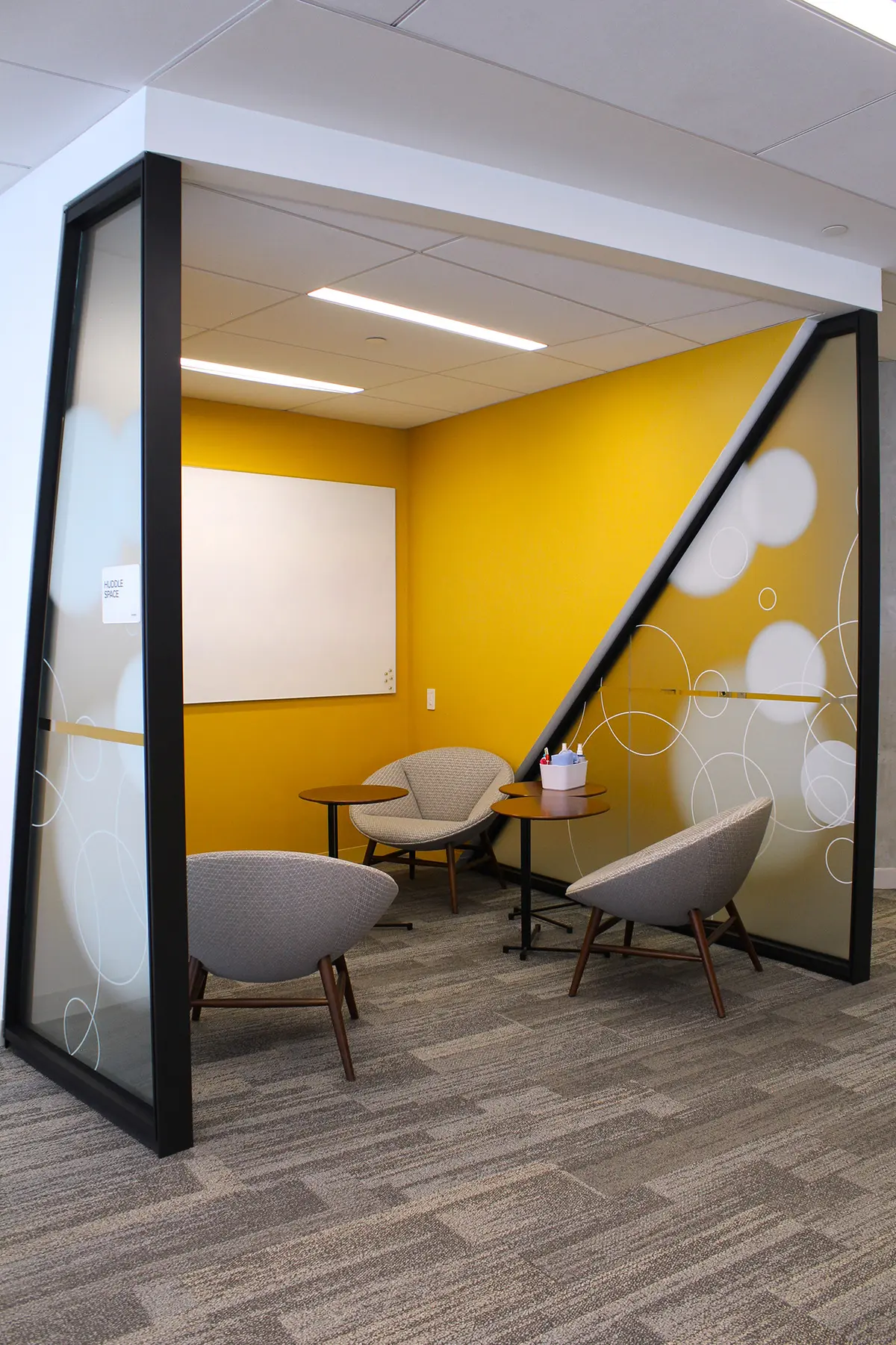
Frequently Asked Questions
About Verto360
About Verto360
Verto360 provides comprehensive services for your construction projects, encompassing every stage from initial concept to execution. This includes budget planning, innovative design, and efficient construction management. We collaborate with trusted consultants and contractors to ensure a seamless experience and are open to partnering with your preferred professionals as well. We also offer post-construction services, which extend to sustainability reporting, relocation assistance, and adaptive modifications to meet your evolving space requirements, all aimed at enhancing your long-term success.
Verto360 specializes in a variety of sectors, successfully executing construction projects for:
- Higher Education Institutions (universities and colleges)
- Healthcare Facilities (acute care, clinical and office spaces)
- Municipal and Government Buildings
- Corporate Offices (including legal firms)
- Retail Spaces
The key benefit of partnering with Verto360 is our innovative and streamlined process. Traditional construction projects often involve delays, cost overruns, and site challenges. In contrast, Verto360 offers a cohesive and safe project journey from inception to completion by creating a digital twin of your space early in the process, thereby minimizing change orders and enhancing accuracy. Our advanced software allows you to virtually tour your space before construction, ensuring your project is completed on time and on budget, with precise measurements and smooth on-site installation.
At Verto360, we’re your collaborative construction partners, working with designers and architects upfront as they contemplate creating designs based on prefabricated construction solutions for their projects. We consult on best practice solutions based on our 15 years of experience specifying prefabricated construction solutions, while keeping long-term adaptability and sustainability in mind. Using an industry-leading software, we render the design in a virtual, 3D digital space or plan view before IFT (issued for tender) or IFC (Issued for Construction) drawings are issued. We provide accuracy and transparency with tolerances to the milimetre, detailed elevations, accurate pricing, glass calculations and more. This accuracy and clarity in the design phase eliminates unwanted and unnecessary surprises, change orders and delays during the on-site construction phase. Very few other companies in the construction industry leverage technology in this way, and we pride ourselves on being at the forefront of this much needed industry evolution.
Our Process & Its Advantages
We utilize ICE software, a revolutionary tool originally developed in the gaming industry. ICE enables you to virtually explore your space in 2D, 3D, and virtual reality before finalizing designs and starting construction. This transparency ensures your project stays on schedule and within budget, with clear visuals and expectations from the outset.
Our design and construction timeline is impressively efficient. We require approximately 4-5 weeks for manufacturing preparation. Once materials are ready, our solutions can be installed in roughly 50% of the time a traditional construction project would take. Factors influencing the project timeline include the project's size, exterior work, design process, permit acquisition, and budget approvals. Our project durations have ranged from a swift 8 weeks to more extended timelines, depending on these variables.
With a prefabricated approach, floor finishes and ceiling grids are installed before prefabricated walls go up. Electrical outlets and light switch back boxes are pre-installed in the prefabricated walls, eliminating the need for electricians to cut openings and install device boxes in drywall, or pull cables.
Factory orders for manufactured construction assemblies can be deferred to within 3-5 weeks of arrival on site.
At Verto360, we work with contractors to provide them clear installation timelines, which helps prevent unnecessary work, damange to installed material and delays. This efficient approach can reduce contractors’ labour costs by up to 50%.
In many cases, architects and designers finalize drawings before deciding whether a prefabricated solution is appropriate. This results in extensive re-work to adapt existing drawings and specifications to fit a prefabricated solution. For optimal results, it’s crucial to decide on a prefabricated solution or conventional construction methodology early in the design process to avoid a disjointed specification and unnecessary revisions.
At Verto360, we consult with architects, designers and other project partners from the outset, helping advise on solutions that will ensure efficiency while maintaining the design intent of their plans. We help ensure decisions about demountable solutions are made early on, eliminating the need to adapt or extensively rework their drawings.
We can also help determine the ideal specifications, like glass thickness. Architects and designers often specify 10, 12 or 13mm thick glass based on conventional stick-built glazing solutions. However, a unitized solution can achieve a similar aesthetic without sacrificing acoustical performance with thinner glass. In other words, our our solutions can in many cases offer the same high-quality aesthetic with thinner glass, making for a more cost-effective option.We’re always happy to consult with architects and designers early on to ensure the correct glass thickness is specified.
Additionally, DIRTT wall assemblies include built-in leveling capabilities, eliminating the need for costly floor leveling. These are just a few examples of the ways we work to make architects and designers’ experiences more seamless and bring their plans to life.
These are just a few examples of the ways we can work to make architects and designers’ experiences more seamless and bring their plans to life without extensive revisions and pitfalls.
Some of the common challenges contractors face on-site are labour shortages, inconsistent workmanship, re-work, extended lead times for materials and coordination of trades and products. With prefabricated construction, components consisting of several trades, including all frames and small parts, are pre-assembled off site as part of the manufacturing process - meaning they can be installed by a much smaller crew on site. This reduces the need to hire and coordinate individual trades and streamlines the construction process significantly.Manufactured construction provides a consistently higher level of fit and finish than individual trades on-site can achieve. Additionally, manufactured construction reduces lead times to 3 -5 weeks for complete assemblies.
About Prefabricated Construction
Prefabrication refers to an approach where components are pre-built and then transported to the construction site, enhancing efficiency, quality, timelines, and cost-effectiveness. Prefabrication often integrates multiple trades into a single solution, streamlining the construction process. This umbrella term is used interchangeably with various construction approaches and terms, including prebuilt, modular, manufactured, and demountable solutions.
Prefabricated construction essentially refers to a process where certain elements or structures are pre-built off site and then transported to the construction site for installation. Prefabricated components could include entire structures, like homes or modular buildings, or smaller subsystems like HVACs or bathrooms, for example. The materials used can be similar to those used in on-site construction, or they can be alternative selections. One advantage of this approach is that it combines multiple trades or aspects of construction into one solution. The main goal of prefabricated construction is to enhance efficiency, quality, timelines and cost-effectiveness.
Technology continues to advance, and so do prefabrication methods. These ongoing innovations are revolutionizing the construction industry and fundamentally changing the way individuals and corporations are tackling these projects.
Demountable simply means a component of your space that’s designed to be taken down, moved or reconfigured as needed. While many clients initially don't anticipate the need for this kind of flexibility, approximately 60-90% find themselves reconfiguring their spaces eventually.
Flexibility is a fundamental characteristic of prefabricated construction. While it provides certain design and construction parameters, it offers substantial flexibility in design, manufacturing, installation, sustainability, and adaptability. This approach also allows you to reconfigure your space as your needs evolve.
Prefabricated construction is inherently sustainable. This approach ensures fixed pricing, supply integrity, minimal waste, reusable elements, and superior fit and finish, unlike many traditional construction methods. We provide a sustainability statement for each project, detailing environmental benefits like reduced drywall use, off-gassing prevention, recycling efforts, and amount of bio-based materials used.
Yes. The Canada Revenue Agency (CRA) classifies prefabricated construction as a class 8 asset, depreciating at 20% per year, allowing for full write-off within 5 years. In contrast, conventional construction materials are classed as class 1 assets, depreciating at 4% per year over 25 years. Actual savings vary based on the project and the corporation's marginal tax rate. We recommend you consult with a tax professional or accountant for tailored financial advice.
Prefabricated construction significantly reduces health and safety risks associated with traditional construction. It minimizes exposure to silica dust, off-gassing from on-site paint, and infection risks through non-porous, washable surfaces that meet healthcare standards. Additionally, it reduces noise pollution and enhances workspace acoustics, while CSA-approved electric components ensure safety against electrical hazards.
Have more questions?
Contact us if you'd like more information, or to schedule a free consultation.
Contact Us