Insights from verto360
How To Be As Inefficient As Possible
Andrew Lutowicz, President, Verto360
December 2, 2024
Maybe it’s our mindset about prefabrication, or our tendency to think in terms of pre-assembled assemblies, or maybe it’s just common sense.
When we think of a wall with a door in it, we inherently believe that the door, its hardware, the wall, and door frame should all come from one vendor. The architect is responsible for the specification and for meeting code, but that vendor should be accountable for the door’s assembly and functionality.
But that’s not how it works in the real world of construction.
On many projects, the supplier for each component of the door could each be separate vendors or trades. To the point where sometimes, portions of the assembly can be constructed by non-union trades and others must be by unionized trades, for example.
I think you can see where I’m going with this. It is a co-ordination nightmare. And it’s spelled “change order” or “cha-ching!”
If you take a look at these photos, you’ll see a perfect example.
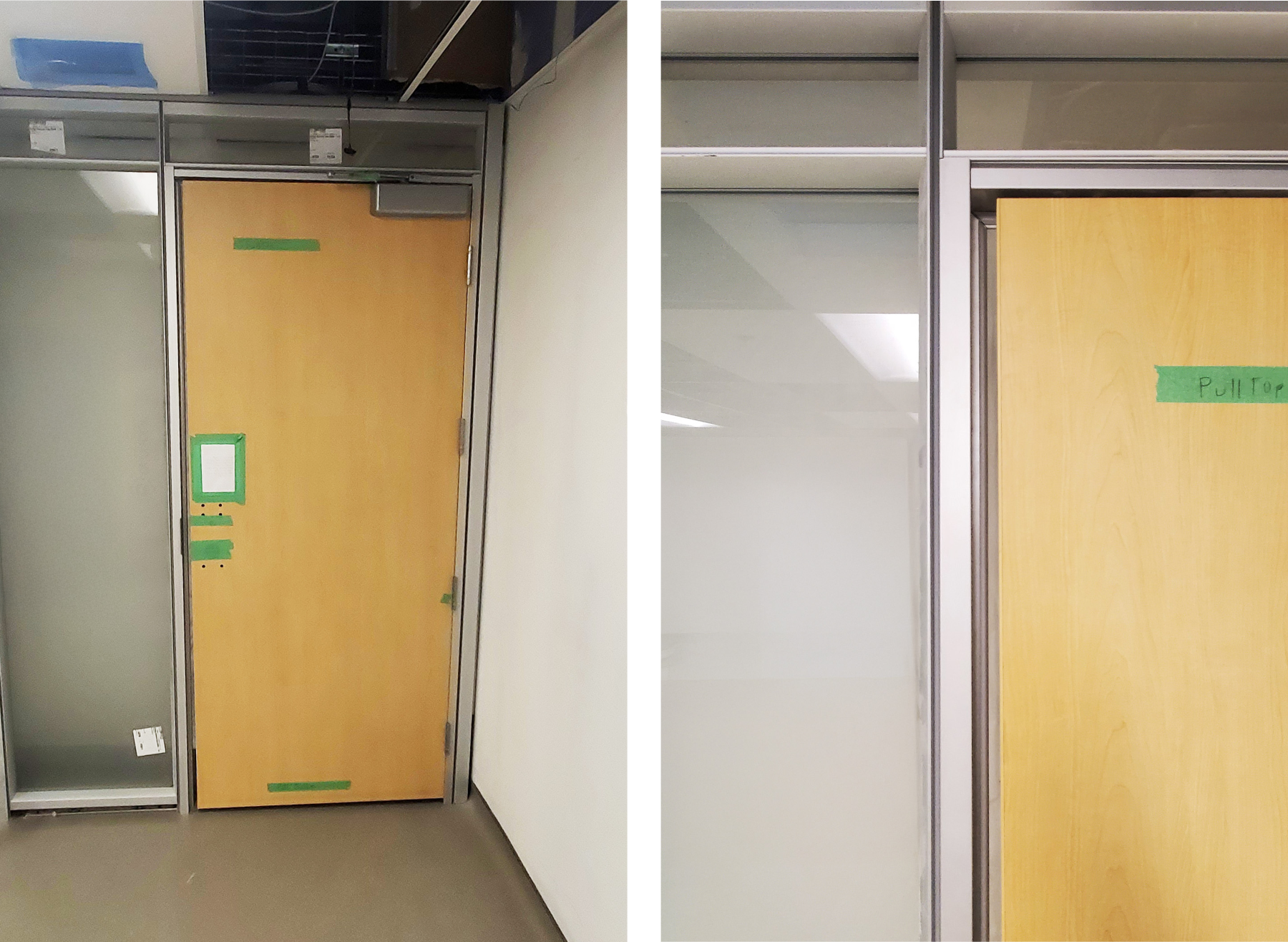
This is a hospital with a multi-year project coming to conclusion.
The trades involved are:
- Verto 360, who provides and installs the wall and door frames. We’re also responsible for milling out the door frame for hardware which will be supplied by another vendor.
- Vendor B, who supplies the door slab, per architects’ specifications.
- Vendor C, who supplies and installs the door hardware, per architects’ specifications on the frame and slab
But oops! The door slab is one inch too narrow for the door frame.
How did this happen?
- Did the door slab manufacturer build the door slabs the wrong size?
- Did Verto360 order and build the door frame too wide?
- Did the architect provide the wrong information to either Verto360 or the door slab manufacturer, or both?
And most importantly, who do you think is going to foot the bill?
Here’s the even bigger problem. The general contractor is supposed to hand over the project to the hospital for occupancy in about 6 weeks. It takes 3 to 12 months to get door slabs manufactured and there’s no way a building inspector is going to issue an occupancy certificate with doors like this.
And that’s just one logistical nightmare that’s unfolding.
The hardware manufacturers’ specifications have changed, but that hasn’t been communicated to the door frame manufacturer or the door slab supplier. Their products arrive on-site, pre-milled for the original hardware specifications provided, and the new hardware doesn’t fit!
Door hardware takes months to get, and on a project with a multi-year timeline, what happens if that particular hardware has been discontinued?
Who is at fault? Who should pay?
With pre-engineered, prefabricated construction and assemblies, this insanity can be avoided.
I rest my case.
Ready to experience a better way to build? Get in touch with us to chat more about it.